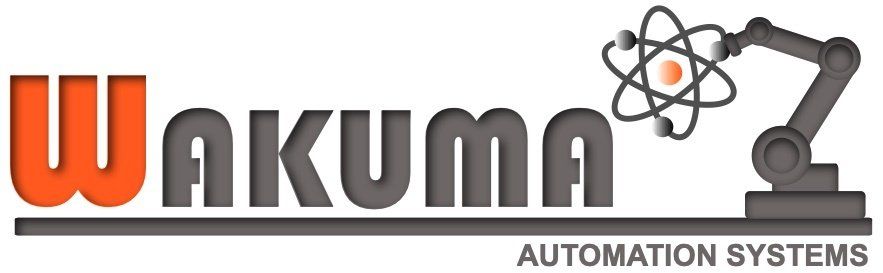
Products and services
Sample preparation
Sample milling machine with variable single spindle and 6-fold changer
W-ESF-11
Use
This milling machine is designed for the toughest use in harsh environments. Depending on the application, it can be offered with different spindle capacities and speeds. It is therefore suitable for light metals as well as for the hardest steel and pig iron samples (up to 67 HRC) to prepare the surface for spectrometry or X-ray fluorescence analysis. You can automatically, for. E.g. with robots, conveyor belts, linear slides and also manually loaded.
Integration and operation
The machine can be loaded from 3 different sides, making it ideal for integration in automated areas and robot circuits. The location of the input and output of the sample can be variably defined via the interface during operation when the higher-level control registers. This flexibility offers enormous advantages in larger laboratories with high sample throughput and multiple routes to analysis. The interface is precisely matched to the application areas. The standard is the connection via Profinet, others are also possible by arrangement.
The machine is controlled by a fail-safe Siemens S7-1500F PLC. Operation is graphically oriented, user-friendly and understandable, so that even inexperienced staff can quickly familiarize themselves with it. A mobile panel can be taken to the place where it is needed for adjustment work. The integrated enabling button offers the necessary security when manually executing drive movements in setup mode. Up to 64 different programs with adjustable spindle speed, feed and chip thickness can be created. A sample can run through up to 6 milling cycles, even with different tools per milling.
Robustness and tools
The milling spindle is equipped with a high-quality precision bearing. In conjunction with the heavy, stable design of the machine body, the axis guides and the clamping unit, all vibrations are reduced to a minimum, even with very hard samples. This has an above-average effect on the milling pattern and guarantees an even surface and reproducible roughness for the subsequent analysis. The quality axis drives have a guaranteed positioning accuracy and stability of 1/100 mm. There are six storage locations for tools for automatic changing, which can be equipped with different cutting inserts.
Mix-up check
-Sturdy steel housing, with maintenance openings, painted.
- Slider on the top to close the outlet opening, pneumatically operated.
-Grinding unit for pre-treating the surface before measuring.
-X/Z axes for horizontal and vertical movement of the
Spark probe in a stable design with parallel linear guides, ball screw, driven by servo motors. This type of drive has the advantage that the spark probe can be moved smoothly through targeted acceleration and deceleration, which significantly minimizes wear and tear on the sensitive electronics in the spark probe.
-Integrated electrode cleaning with electrically driven
Cleaning brush, various blowing nozzles clean the head and the light entry window of the spark probe.
-Air cooling of the electrode, after each measurement the electrode is cooled with compressed air.
-Automatic approach to maintenance positions
-Up to 5 different measuring positions can be approached, the distance between the measuring points can be set via the control
be freely parameterized.
Analysis systems
Use
Our standard analysis system ideally combines sample preparation and analysis with spectrometry in the smallest of spaces. The milling machine W-ESF-11 is used in connection with a spectrometer in the upper performance range. The standard analysis system can be ordered complete as a container or for installation in the laboratory area. The composition of the components are tailored to your needs and requirements. The container version offers the unbeatable advantage that there is no longer any need to transport the samples to the laboratory. The analysis result is available much more quickly and for this reason ensures a higher production capacity and extends the service life of the lining through faster casting. This investment pays for itself in a very short time. The interfaces can be flexibly adapted to the respective plant control system, so current melt numbers and other parameters can be sent from the plant to our system and displayed on the terminal for selection. After the analysis, the results are immediately transmitted to the plant control system or LIMS.
Integrated, freely configurable control and recalibration samples allow self-checking of the analytical accuracy and recalibration of the system.
integration and operation
A panel PC offers an overview of the entire system with its software (W-LabOs) with a graphic interface, it is used for parameterization and administration of the control and recalibration samples. The self-test and the recalibration are carried out by a freely selectable schedule. An internal database saves all analysis results. All communication to the spectrometer and plant control system as well as error messages and operator entries are saved in log files.
Other features:
- Temperature measurement of the sample
- Height measurement of the calibration and control samples
- Camera to check the sample surface for blowholes
- Optional radioactive measurement
- Signing by label, embossing or lasering
- Company samples can be returned for reuse
- The input location of the sample can be specified by the customer
Lab control systems
Depending on the application, the modular software and the interfaces are precisely adapted to the needs of the customer and the system.
Our specially developed laboratory organization system (PC software) handles the communication and control of the various analysis devices. The system saves all results in an internal database and creates the interface to higher-level factory systems (e.g. LIMS). The analysis results are processed and transmitted using the plant's existing log. The software also provides the interface to the operating and monitoring personnel (HMI). It offers an overview of the entire system, displays any errors that occur and is responsible for entering all parameters.
Update service
Do you have a system with solid, functioning mechanics, but the control technology and software no longer meet the requirements of today's industrial age?
We can offer you an individual update to the latest technology, operating systems and software. This means that you can continue to use your proven technology with new functions and options with little financial outlay.
Contact us.
Service and control update for old Pfaff systems
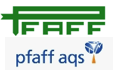